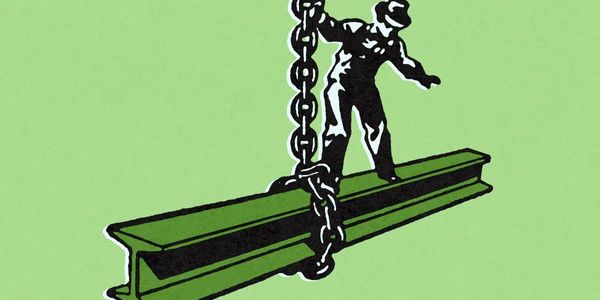
Energy use in the iron and steel industry accounts for about 7% of global greenhouse gas emissions — that’s more than it takes to power commercial buildings, more than twice the emissions of the entire cement industry, and nearly four times as much as the aviation sector. Steel-related emissions are so high primarily because melting and refining iron ore, the base metal of steel, requires extremely high temperatures, which has typically come from burning coke — derived from coal — in blast furnaces.
Electra, a Colorado-based startup, is building momentum around a low-temperature electrochemical approach to iron refining that stands to drastically reduce emissions, and on Thursday announced a $186 million Series B funding round. The company’s battery-like devices would electrify the steelmaking process while their relatively small size could move the industry towards a more modularized, “Lego block” approach, negating the need to build a huge facility all at once.
If it works, there’s a lot of money to be made. “The steel industry is so big,” Electra’s CEO, Sandeep Nijhawan, told me. “We're talking about a $1 trillion a year market, and something like $600 billion of iron-making that has to happen every year.” The company’s latest funding round was led by the Singaporean investment firm Temasek Holdings and the sustainable investment firm Capricorn Investment Group.
Electra can refine iron at just 60 degrees Celsius — cooler than your average cup of coffee and orders of magnitude cooler than the 1,600 degrees Celsius that traditional steelmaking requires. This low-temperature approach is particularly conducive to working with renewables, as the process can be easily started and stopped in tandem with the availability of wind and solar resources. That’s not the case for high-temperature systems such as the one used by green steel startup Boston Metal, which works with molten ore that must be kept extremely hot at all times, lest it harden.
First, Electra’s process involves dissolving iron ore in an acidic solution at near room temperature, which separates the iron from impurities in the ore such as alumina and silica. Then an electric current is passed through the solution, which causes a chemical reaction that deposits the pure iron onto stainless steel sheets, a much lower-temperature process than refining iron in a blast furnace. Electra’s steelmaking partners then convert the sheets of iron into steel via an electric arc furnace, which has the potential to be nearly emissions-free if powered by renewables.
The process isn’t actually so different from the way other metals such as copper, zinc, nickel, or cobalt are produced, Nijhawan told me, and it allows Electra to use contaminated or low-grade iron ores that would otherwise be ill-suited to low-carbon steel production.
The reason it’s taken so long to figure out how to refine iron ore the way we’ve been refining other metals for centuries is because iron can be particularly difficult to work with. For one, it takes a whole lot longer to dissolve in acid than other common metals; one of Electra’s breakthroughs was finding a proprietary way to pre-treat its ores so that they would dissolve more quickly. Secondly, once the iron eventually dissolves, it’s no longer stable, and tends to fall out of the solution before all the impurities are removed. Figuring out how to stabilize the ore by changing its oxidation state was another one of Electra’s breakthroughs. “Putting that system-level package together is where our innovation is,” Nijhawan told me.
This latest funding round will help finance the construction of Electra’s demonstration plant in Colorado, where it already operates two pilot plants powered with 100% clean energy, procured via a renewables program from the local utility, Xcel Energy. The company’s demo plant, which should be operational by early next year, will also run on renewable power from Xcel, while its first commercial plant, planned for the end of the decade, will either be located in an area with high renewables penetration or be powered with help from renewable energy partners, Nijhawan explained.
“Eventually when this scales, you will purpose-build the renewables infrastructure to feed the plant,” Nijhawan told me. Some of the biggest strategic investors in the space have bought into this model of steel decarbonization, including three large iron ore companies — Rio Tinto, BHP, and Roy Hill — as well as two large steel producers — Nucor and the Japanese company Yamato Kogyo. Prominent climate tech investors such as Breakthrough Energy Ventures and Lowercarbon Capital also invested.
Once the process scales, Electra expects its iron to reach cost parity with traditional processes. Scaling-up, of course, is the tricky part, especially as tariffs and the generalized atmosphere of uncertainty is making infrastructure investors clam up when it comes to betting on large, first-of-a-kind projects. Nijhawan told me that so far, Electra’s scale-up strategy that he laid out last year remains unchanged.
“We are trying to replace how iron has been made for centuries with electro-iron, hopefully for decades to come”, he told me, explaining that in this moment of uncertainty, it helps to take the long-term view. “We now have this broad set of investors. Some of them have a 100 year history, they have deep manufacturing experience, and have been through administrations and policy changes. You just have to build a strategy that's built to last.”